SimLex Series
Sales Control
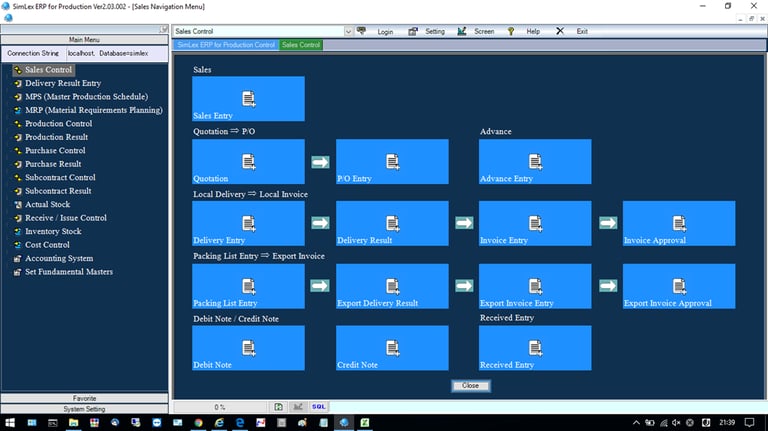
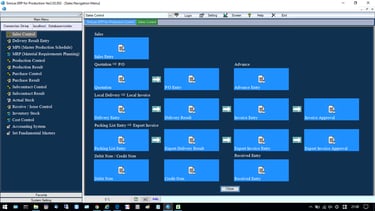


Basic business flow is Quotation → customer's P/O input →
Delivery Note → Delivery result → Invoice input. Customer P/O and Invoice are needed to Approve.
Users can make a Quotation. If Item code dose not exist in Item Master, Item will be created automatically. After Quotation is created, Users can enter automatically from a Quotation.
After you enter Customer P/O, Users can enter Delivery data and print Delivery Note. Users can spirit delivery quantity or enter plural Customer P/O as 1 Delivery Note.
Users can print Invoice according to Delivery Note.
Users can enter Advance. Debit Note or Credit Note is used for unit price adjustment.
P/O, Delivery Reports are Confirm P/O Report, P/O Back Order Report, Weekly Delivery Schedule Report, Monthly Delivery Schedule Report.
Accounting Receivable (AR) Reports are AR History Reports, Aged Receivable Detail / Summary, Debtor Card.
Actual Sales reports are Actual Sales by Item, Actual Sales by Customer
Purchase Control
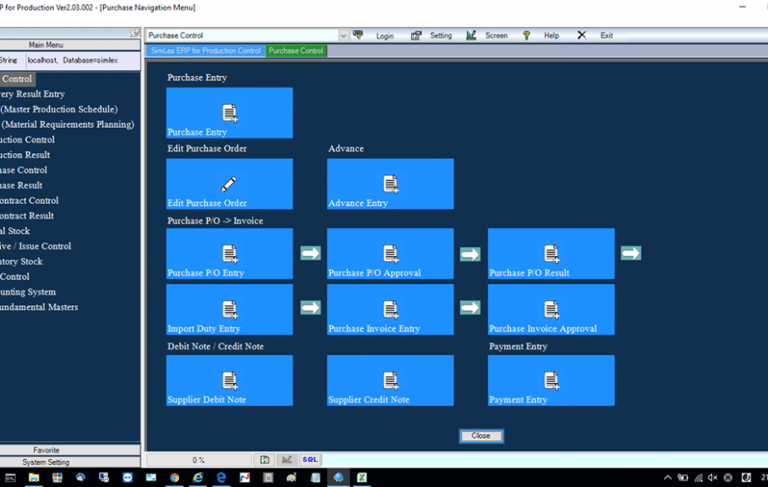
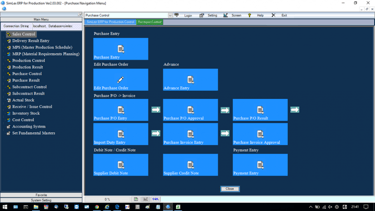


Basic business flow is P/O Entry / Report → P/O Approval → Received Result Entry → Supplier Invoice Entry → Invoice Approval.
SimLex supports foreign Currency and you can enter P/O. Purchase Price Mater supports expired date and unit price by lot size.
After P/O is entered and printed, you can enter received result. SimLex supports to split received quantity.
Users can enter Advance, Debit Note or Credit Note. Debit Note or Credit Note is used for unit price adjustment.
Purchase Reports are P/O Back Order Report, Merchandise Received Sheet for Item, Monthly Receive Schedule Report.
Accounting Payable (AP) Reports are AP History Reports, Aged Payable Detail / Summary, Creditor Card.
Actual Purchase reports are Actual Purchase by Item, Actual Purchase by Supplier.
Production Control
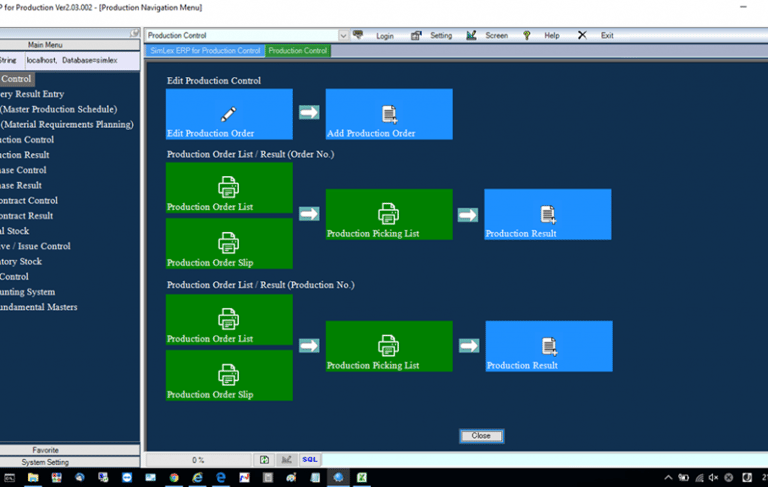
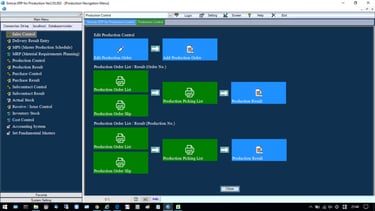


Basic business flow is Release Order after MRP or Additional Order → RM Picking Result Entry → Production Result Entry.
After Release Order by MRP, users can print Production Order List (By Order No. or Production No.).
Users can print Picking List (By Order NO. or Production No.). And users can enter Picking Result.
If production is finished, you can enter Production Quantity, NG Quantity, Lot No., Location. At the same time of production entry, users can enter the Defectives.
If Production Result is entered by Lot No., you can execute Lot Trace and Actual Stock by Lot No..
Production Control reports are Production Slip, Back Order List, Production Result list.
Need the best solutions for your company problems?
Please contact us
ContaCT Us:
info@c2mfg.biz
+62 21-251-2663
Address:
PLAZA SENTRAL 19 Floor,
Jl. Jend. Sudirman No.47,
Jakarta 12930 - Indonesia
PT. C2MFG Indonesia